
Scientists have long been intrigued by the durability of Roman-built buildings. For instance, the famed Pantheon, which has the world's largest unreinforced concrete dome, was built in 128 CE and still stands today. A Roman-era aqueduct, the Aqua Virgo, built of the same concrete, still supplies water.
A little over a year ago, Massachusetts Institute of Technology Professor Admir Masic and his Italian and Swiss collaborators published a startling discovery about the concrete used in ancient Rome. The researchers uncovered the presence of so-called lime clasts—granules of calcium carbonate that gave concrete self-healing properties—according to their paper published in the journal Science Advances.
The key was using hot mixing of quick lime (a reactive form of calcium that generates heat on mixing with water) instead of slaked lime (a cooler, slow-acting form). Because of the presence of the resulting lime clasts, cracks formed in concrete could heal themselves when they came in contact with moisture and pozzolanic materials, such as volcanic ash contained in the mix.
Ticking Time Bombs
Emerging knowledge like this could have incalculable value. Since English bricklayer Joseph Aspdin invented and patented Portland cement in 1824, reinforced concrete has been used worldwide in buildings, highway bridges, offshore platforms, dams, roads, etc. The typical service life of such structures is expected to be 50 years on average and up to 200 years if built with extra care and special provisions.
Compared to concrete used in the Roman period, the massive infrastructures built in the last couple of centuries are ticking time bombs.
However, compared to concrete used in the Roman period, the massive infrastructures built in the last couple of centuries are ticking time bombs. They require frequent repair and maintenance during their service lives. They will also eventually need to be demolished or rebuilt.
There is an environmental impact, too: The buildings and infrastructure construction sector is estimated to contribute around 40% of greenhouse gas emissions in terms of embodied and operational carbon footprint, according to the UN Environment Programme and its Global Alliance for Buildings and Construction.
The race is now on to use this new knowledge about “self-healing” concrete and modify modern-day concrete to mimic the longevity and much lower carbon footprint of the ancient construction material.
The Need for Resilience
Resilience is the ability of any structure to withstand extreme load events, such as an earthquake, typhoon, explosion, etc., and recover from it as quickly as possible. The frequency of extreme natural (see Figure 1) and man-made disaster events, such as hurricanes, storms, floods, earthquakes, tsunamis, heat waves, fires, terrorism, etc., has been increasing in recent decades.

It has underscored the need for durable, safe, and securely built infrastructure. As a tragic example, a magnitude 7.8 earthquake hit the Turkey-Syria region on February 6, 2023. More than 160,000 buildings were destroyed or severely damaged, and more than 53,000 people died. Some 2.7 million were left homeless.
War-torn Syria is estimated to have 40 million tons of cement rubble, in addition to the cement debris from the 2023 earthquake. According to a 2023 article in The Guardian, which cited a study in the Journal of Materials in Civil Engineering, efforts are underway that demonstrate how to prepare—and strengthen—local rubble to rebuild the nation.

New Lower Carbon Footprint Material
In recent years, there has been a concerted effort to reduce the environmental impact of cement production as rapid urbanization occurs in Asia and Africa (see Figure 2).

Traditional Portland cement contributes significantly to carbon dioxide emissions (around 5% to 8% of the global emissions). Its production requires an energy-intensive process to create clinker, composed of mostly limestone, that is then ground into cement powder. However, several lower-carbon alternatives to clinker are now available.
Pozzolanic Cement Concrete
Historically, supplementary cementitious materials (SCMs) have long been used in construction. The Romans used volcanic ash, while other parts of the world used various forms of reactive clay, etc., as a supplement to the primary binder, such as lime and, more recently, cement.
Supplementary cementitious materials (SCMs) have long been used in construction; the Romans used volcanic ash.
SCMs, or pozzolans, are materials with weak binding properties in the presence of water and calcium hydroxide resulting from the primary reaction of cement or lime. Modern industrial byproducts—such as fly ash (a coal combustion residue from thermal power plants), slag (residue from the blast furnace), and silica fume (residue from the ferro-silicon industry)—can be used as partial replacements for Portland cement.
Incorporating SCMs reduces the need for clinker production, resulting in lower carbon dioxide emissions. In countries like China and India, higher quantities of SCMs are incorporated directly in the cement-making process itself to make products like Portland Pozzolanic Cement (PPC), Portland Slag Cement (PSC), and composite cement (using both fly ash and slag). Besides reducing embodied carbon and reducing waste, SCMs improve the long-term performance and durability of concrete structures.
Despite their advantages and potential, these emerging SCMs do have their drawbacks and limitations when compared to Portland cement. For instance, there may be problems with incomplete dispersion of some composites throughout the mix, as well as increased water consumption requirements which can affect workability, among other issues. As these SCMs are relatively new, there is also an obvious lack of testing of some for their long-term mechanical properties.
Geopolymer Concrete
One of the primary sources of greenhouse gas emissions in Portland cement manufacturing is the high-temperature process of producing clinker from limestone and clay.
If one can imagine a room-temperature process to make Portland cement without using limestone, then geopolymer cement would be that wonder material. It is produced by activating aluminosilicate materials, such as fly ash or slag, with a strong alkaline solution.
This alternative cementitious material offers comparable or even superior mechanical properties compared to Portland cement-based concrete. Geopolymer concrete has a significantly lower carbon footprint and exhibits excellent resistance to fire, chemicals, and fatigue. Unfortunately, Portland cement production approaches over 4 billion tons a year—making Portland cement concrete the second-most-used material by humans (after water). This leaves an insufficient amount of pozzolanic source material available to meet demands by geopolymer concrete alone.
Limestone Calcined Clay Cement (LC3)
In South Asia, the Bureau of Indian Standards (BIS) last year released an exclusive Indian Standard (IS 18189: 2023) for a new type of low-carbon cement called LC3. This cement is produced from about 50% Portland cement clinker, 30% calcined clay, 15% limestone, and 5% gypsum. Among the various new cement formulations, LC3 has been the most successful emerging commercial product in several countries. Each ton of calcined clay produced saves 600 kilograms (1,322 pounds) of CO2. By the end of 2025, it is expected that LC3 will have saved 45 million tons, according to the Swiss-supported LC3-Project.
Real-Life Examples
High-volume pozzolanic concrete made from PPC, PSC, and composite cement is commonplace in every type of construction where ordinary Portland cement concrete is used. The same is increasingly the case with LC3 cement-based concrete.
New cementitious materials have undergone extensive testing and have also been successfully utilized in pavements, retaining walls, water tanks, and precast bridge decks.
The University of Queensland's Global Change Institute (GCI) has been constructed using geopolymer concrete. It is a four-story building for public use and is claimed to be the first of its kind. New cementitious materials have undergone extensive testing and have also been successfully utilized in pavements, retaining walls, water tanks, and precast bridge decks.
Ultra-High-Performance Concrete
Several cementitious materials show significant promise in terms of disaster resilience. Ultra-high-performance concrete (UHPC), for example, is a material that has outstanding mechanical properties. It offers high strength, ductility (can be shaped without losing strength), and energy absorption capacities, making it suitable for blast-resistant structures. UHPC can withstand extreme loads and impacts. It is an ideal choice for structures exposed to potential terrorist attacks.

UHPC consists of carefully chosen ingredients based on particle-packing principles to give a dense microstructure that is further reinforced with micro-steel fibers. It is also known as reactive powder concrete (RPC) or densified system of particles (DSP). Its dense microstructure provides impact resistance, high strength, and excellent durability properties, providing extended service life.
Fiber-Reinforced Concrete and Engineered Cement Composites (ECC)
As their names suggest, fiber-reinforced concrete (FRC) and engineered cement composites (ECC) are composites that combine fibers with cementitious materials with a range of strength, ductility, and durability properties. They can be designed to help resist impact and energy absorption capacities. By incorporating fibers, these materials can effectively distribute and dissipate energy during extreme load events, reducing the potential for structural failure.
ECC has resulted from the pioneering work of Professor Victor C Li and his co-workers at the University of Michigan, based on a design framework illustrated in Figure 3. Their approach considers multi-hazard extreme load conditions—such as a levee breaking apart in an earthquake or hurricane—and the future impact of climate change-induced increases in loading. The goal is to develop an optimal design that can justify the initial investment in high-performance materials such as UHPC or ECC, which can provide the desired level of resilience and sustainability.
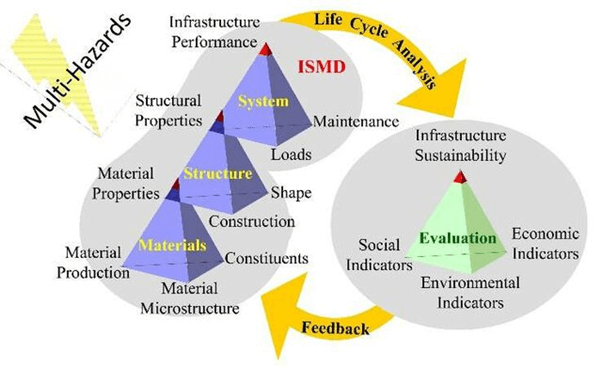
While many real-life applications of UHPC and ECC are available in almost every type of construction project, their adaptation needs to be more widespread. The increased availability of these materials for use depends on various factors, including research and development, standardization, production scalability, and market demand. While some of these materials are commercially available, others are still in the research and testing phase. Advancements in these materials are expected to continue, and their availability is likely to increase in the coming years as their benefits are recognized and demand grows.
Towards a Safe and Sustainable Infrastructure
Developing and adopting new cementitious materials with a lower carbon footprint and enhanced disaster resilience are crucial steps toward sustainable and safe infrastructure development for the future. These materials offer superior performance during natural disasters, such as earthquakes, typhoons, and explosions, while reducing the environmental impact of traditional Portland cement.
Geopolymer concrete, limestone calcined clay cement (LC3) concrete, ultra-high-performance concrete (UHPC), and fiber-reinforced composites (FRC) are promising materials. As awareness grows and regulations focus on sustainability and resilience, adoption of these materials is expected to increase, contributing to a more resilient and environmentally friendly construction industry.
*Dhanada K Mishra has a Ph.D. in civil engineering from the University of Michigan and is currently based in Hong Kong, working for an AI start-up, RaSpect (www.raspect.ai). He writes on environmental issues, sustainability, climate crisis, and built infrastructure.
Comments