Is Current Battery Technology Sustainable?
- Nnamdi Anyadike
- Apr 20, 2022
- 5 min read
Updated: Jun 29, 2023
The lithium-ion (Li-ion) battery market has been growing at an extraordinary pace over the last 10 years and will continue to grow at least at the same pace over the next 10 years. Batteries in electric vehicles (EVs), both light and heavy duty, are among the main growth drivers. In 2030, they are expected to represent 77% of the total installed Li-ion battery capacity, up from just 51% in 2019, according to the latest reports.
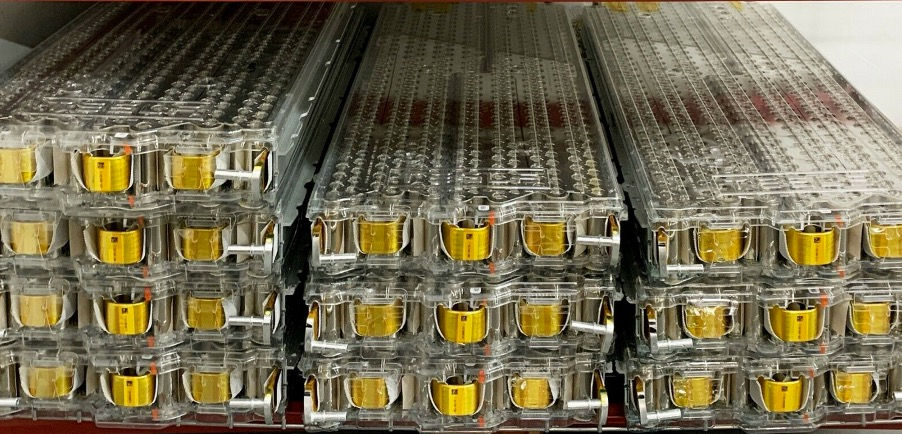
Over the coming years, several changes are expected in the EV market that will affect both the reuse and recycling of batteries. These include the introduction of new battery technologies, the emergence of autonomous vehicles (AVs), and new ownership models of both vehicles and batteries. However, the volumes that will reach end-of-life will grow slower than the volumes placed on the market, because new applications, and their batteries, will last significantly longer than previous applications.
Inevitably, questions arise about the impact of the production, use, and recycling or final disposal of Li-ion batteries. The 2021 “lithium-ion battery life cycle report,” says that recycling “is complicated” and could become even more so if the task of disassembling the components is made too burdensome by heavy-handed regulations. It may also be wasteful. The report predicts, “In 2030 the total amount of Li-ion batteries that will go to reuse will be 145 gigawatt hours (GWh) or 799,000 tons, while 170 GWh or 820,000 tons will be available for recycling.” Nevertheless, while this might look like more batteries are going to recycling than to reuse, most of the recycling will be in batteries with shorter life cycles such as cells and packs in portable devices and personal mobility vehicles.
Recycling Challenges Remain an Obstacle
Six main types of lithium batteries are in use today, each with varying degrees of recyclability. The Lithium cobalt oxide (LCO) battery is most used in small portable electronics, such as mobile phones, tablets, laptops, and cameras. In EV batteries, variations on Li-ion chemistry, including lithium iron phosphate (LIP), lithium-manganese spinel, and lithium vanadium oxide, predominate. The long-life LIP battery is increasing in popularity. These batteries are capable of lasting at least 10 years and undergoing more than 7000 charge/discharge cycles.
Nevertheless, even longer life spans are in the pipeline. LG Chem claims that its lithium-manganese spinel battery can last up to 40 years. The lithium vanadium oxide battery is another example of long-life EV battery innovation with a 10–20-year lifespan that has already made its way into the Subaru prototype G4e.
Although recycling Li-ion batteries will become hugely important as EVs continue to gain traction, there remain sizable logistical and safety challenges in battery recycling.
Although recycling Li-ion batteries will become hugely important as EVs continue to gain traction, Zachary Baum, a Scientific Content Engineer at the Ohio State University’s College of Arts & Sciences (CAS), says that there remain sizable logistical and safety challenges in battery recycling. The first challenge is the transportation of end-of-life batteries from disposal sites to a recycling facility. “This can be expensive if long distances or international transport is required,” he told Supply Chain Digital.
The second challenge is safety. “A 1,000-pound EV battery is highly flammable,” Baum pointed out. “Balancing these issues can make it extremely difficult for battery recycling to be both environmentally efficient and profitable,” he continued. Beyond these two considerations lies the problem of how to efficiently extract the battery’s most valuable metals.
LI batteries are not typically designed with disassembly and recycling in mind and so crushing the device whole is often required. This can be hazardous even though the current generation of LI batteries contain nickel, cobalt, and manganese, which are less toxic than the lead-acid batteries found in most vehicles today. The emergence of the LIP cathode, made without nickel or cobalt, is enabling the creation of cheaper, more stable, and less risky solutions that address both the power and recycling aspects of Li batteries. Tesla has recently announced it will switch to this technology in its lower-range cars.
New Li-Ion Battery Recycling Plants
The German multi-metal supplier and recycling company Aurubis AG announced in March the start of test operations at a new pilot plant in Hamburg. The facility will process the “black mass” from Li-ion batteries. Black mass is a metal concentrate containing nickel, cobalt, manganese, lithium, and graphite that is suitable for hydrometallurgical refining. It comes in the form of a powdery residue. The recovered metals will then be used for new batteries and other products. Aurubis CEO Roland Harings anticipates an investment of approximately US $220 million in a full-scale commercial plant. "I'm firmly convinced that Aurubis will commission an industrial-scale battery recycling plant within the next five years," Harings says.
The German car manufacturer Mercedes-Benz is to collaborate with Primobious to design and construct a battery recycling plant in Germany. The partnership will be conducted through Neometals, Primobious’ 50% owned subsidiary, and the Mercedes-Benz owned subsidiary, LICULAR GmbH. The new plant will be based at Mercedes’ operations in Kuppenheim, Germany, and will mark the automaker’s foray into battery recycling, making it less reliant on raw material supplies in the future. The recovered material will be fed back into the recycling loop to produce more than 50,000 battery modules for the Mercedes’ EQ (Electric Intelligence) range of vehicles.
The plant will have a nominal capacity of 2,500 tonnes per year (or up to 10 tonnes per day) and will be built in two stages. The first stage is expected to commence next year, 2023. Neometals managing director Chris Reed said, “Lithium battery recycling supports the conservation of resources, decarbonization, and supply chain resilience and we are excited to assist Mercedes in its goal to reuse recovered materials.”
Meanwhile, the French mining group Eramet announced in March that it could develop jointly with the environmental services group, Suez, a recycling facility in France for EV batteries by 2024. The company sees recycling as contributing to its potential to cover 20% of the European Union's nickel requirements, 25% of the bloc's lithium needs, and 12% of its cobalt demand for EV batteries by 2030. The two partners are to study various solutions for industrial-scale recycling this year, prior to building the Li-ion battery recycling plant. The facility will produce black mass metal concentrate, and Eramet will look separately at developing a refining plant by 2025-2026 to convert this black mass to battery grade products. Like the planned black mass facility, the refining plant would be located in France.
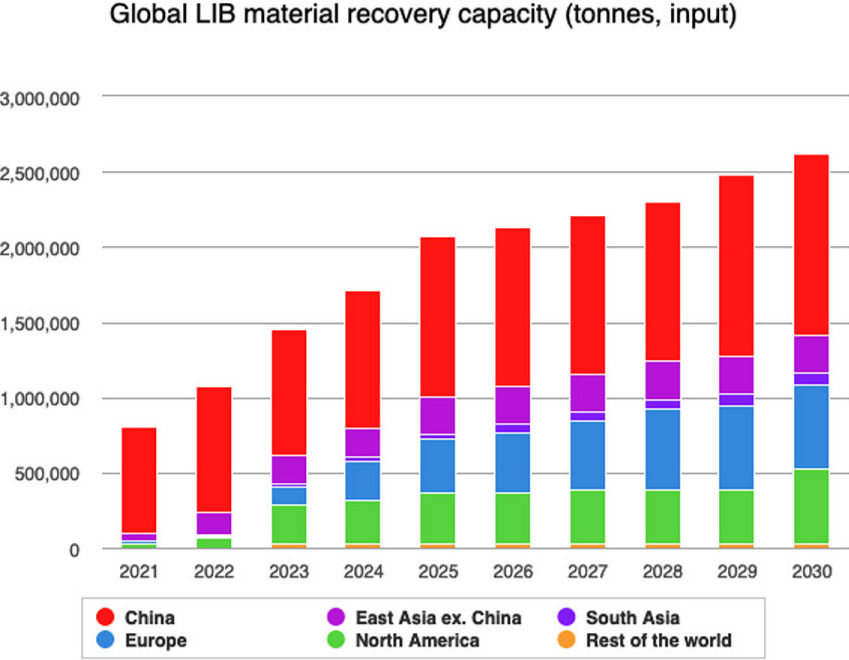
Li-Ion Battery Recycling Prospects
The rapid depletion of primary lithium and cobalt reserves will inevitably force battery manufacturers to move even more decisively in the direction of recycling. All current methods of Li-ion battery recycling are energy-intensive and inefficient. But an alternative approach that is now rising is to disassemble batteries at the end of their useful life instead of shredding them, thereby making new batteries from the old ones. The most recent breakthrough that shows promise in this direction was developed by a team at Princeton NuEnergy. This method to disassemble old batteries and extract their reusable elements relies on the use of low-temperature plasma (ionized gas). As reported by Azo CleanTech, “The Princeton NuEnergy team's strategy eliminates a major portion of international commerce and transportation needs, paving the way for other nations to boost local battery recycling.”
Regulations will also play their part. Today, recycling is not considered a priority for battery manufacturers. But in both Europe and the US, regulations are in the pipeline that will compel battery manufacturers to fund the costs of collecting, storing, and recycling all collected batteries. Appropriate process chains are already being created to ensure the environmentally efficient management of used Li-ion batteries. This will pave the way for a more sustainable future for Li-ion batteries.
*Nnamdi Anyadike is an industry journalist specializing in metals, oil, gas, and renewable energy for over thirty-five years.
Comments